某烘焙企業(yè)曾因一批次產(chǎn)品過期導致客戶投訴,追溯時發(fā)現(xiàn)生產(chǎn)日期與原料批次對應關(guān)系缺失,質(zhì)檢數(shù)據(jù)分散在3個系統(tǒng)中——這種場景揭示了食品行業(yè)質(zhì)量成本控制的深層矛盾:質(zhì)量損失往往源于數(shù)據(jù)割裂而非技術(shù)缺陷。優(yōu)德普的食品加工ERP方案,正通過全鏈路數(shù)據(jù)穿透與動態(tài)根因分析,將質(zhì)量管控從“被動止損”轉(zhuǎn)向“主動預防”。
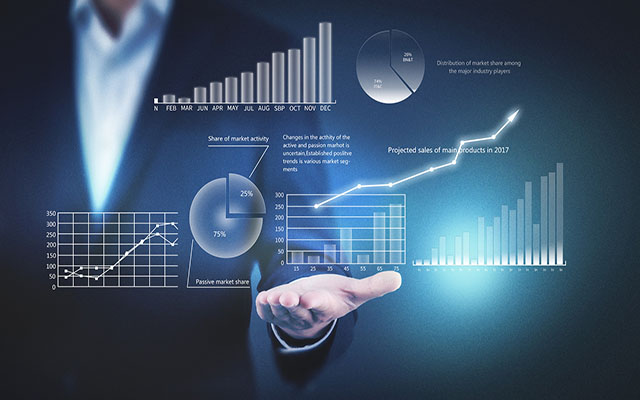
智能追溯:穿透供應鏈的“數(shù)據(jù)顯微鏡”
1.正向追溯:輸入成品批次號,10分鐘內(nèi)可反查原料供應商、生產(chǎn)工單、工藝參數(shù)及質(zhì)檢報告。某肉制品企業(yè)曾借此快速鎖定某批次包裝材料密封性不足導致的保質(zhì)期縮短問題。
2.反向攔截:當某原料檢驗不合格時,系統(tǒng)自動凍結(jié)關(guān)聯(lián)在制品與庫存成品,避免問題擴散至下游環(huán)節(jié),某乳企借此將原料異常處理時效提升40%。
3.合規(guī)性強制管控:在滅菌、灌裝等關(guān)鍵節(jié)點設(shè)置數(shù)據(jù)錄入屏障,未完成質(zhì)檢流程無法流轉(zhuǎn)至下道工序,確保HACCP、ISO22000等標準落地。
對比手工管理模式,優(yōu)德普方案將召回成本降低65%,飛檢報告生成效率提升80%。
不合格品分析:從表象治理到根因挖掘
1.多源數(shù)據(jù)聚合:整合設(shè)備日志(如油炸溫度曲線)、環(huán)境監(jiān)測數(shù)據(jù)(車間溫濕度)、人工檢驗記錄(感官評價),構(gòu)建質(zhì)量數(shù)據(jù)全景視圖。某休閑食品企業(yè)通過分析發(fā)現(xiàn),包裝機溫度波動與真空度不合格率呈強相關(guān)性。
2.根因關(guān)聯(lián)模型:基于知識圖譜技術(shù),建立“設(shè)備參數(shù)—工藝標準—人員操作”的關(guān)聯(lián)規(guī)則庫。當灌裝速度提升15%時,系統(tǒng)自動檢查封口完整性數(shù)據(jù)是否異常,某飲料廠商借此將灌裝不良率從3.2%降至0.8%。
3.成本穿透核算:不合格品損失自動關(guān)聯(lián)至原料成本、人工工時、能源消耗等維度,生成質(zhì)量成本熱力圖。某企業(yè)發(fā)現(xiàn)外包殺菌環(huán)節(jié)的質(zhì)量損失占總成本的31%,遂將部分工序轉(zhuǎn)為自營,年節(jié)約成本超200萬元。
相較于傳統(tǒng)“事后歸因”模式,優(yōu)德普方案通過實時數(shù)據(jù)驅(qū)動,使質(zhì)量問題發(fā)現(xiàn)周期從周級壓縮至小時級。
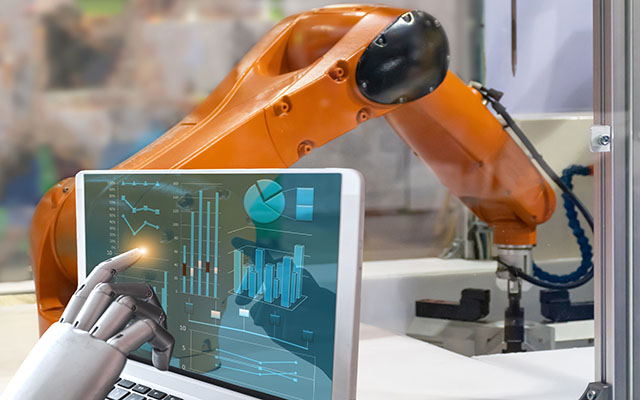
協(xié)同效應:質(zhì)量數(shù)據(jù)與業(yè)務(wù)流的閉環(huán)
1.生產(chǎn)計劃聯(lián)動:當某原料批次不合格率超過閾值時,系統(tǒng)自動調(diào)整生產(chǎn)排程,優(yōu)先使用替代物料,某速凍食品企業(yè)借此減少停工損失15%。
2.供應商協(xié)同:不合格品信息實時同步至供應商門戶,觸發(fā)整改任務(wù)并關(guān)聯(lián)采購合同條款。某烘焙原料供應商因連續(xù)3批次水分超標被系統(tǒng)自動降級,采購轉(zhuǎn)向率提升22%。
3.成本動態(tài)預警:質(zhì)量損失超預算時,自動觸發(fā)跨部門會議通知,推動技術(shù)、生產(chǎn)、采購聯(lián)合制定改善方案。某調(diào)味品企業(yè)通過此機制,將月度質(zhì)量會議決策效率提升50%。
這種“質(zhì)量數(shù)據(jù)驅(qū)動業(yè)務(wù)決策”的機制,使企業(yè)從“單一問題解決”轉(zhuǎn)向“系統(tǒng)性質(zhì)量生態(tài)”構(gòu)建。
1.顯性成本優(yōu)化:手工報表工作量減少60%,質(zhì)檢異常響應時間從48小時縮短至4小時,庫存過期損失率下降35%。
2.隱性能力沉淀:歷史質(zhì)量數(shù)據(jù)轉(zhuǎn)化為預測模型,為新品開發(fā)提供風險預判。某企業(yè)拓展低溫短保產(chǎn)品線時,系統(tǒng)自動提示包裝材料耐冷性測試要求,避免上市后批量質(zhì)量問題。
關(guān)于寧波優(yōu)德普>>>
了解更多SAP ERP管理系統(tǒng)成功案例>>>
或撥打?qū)幉▋?yōu)德普免費咨詢熱線:400-8045-500